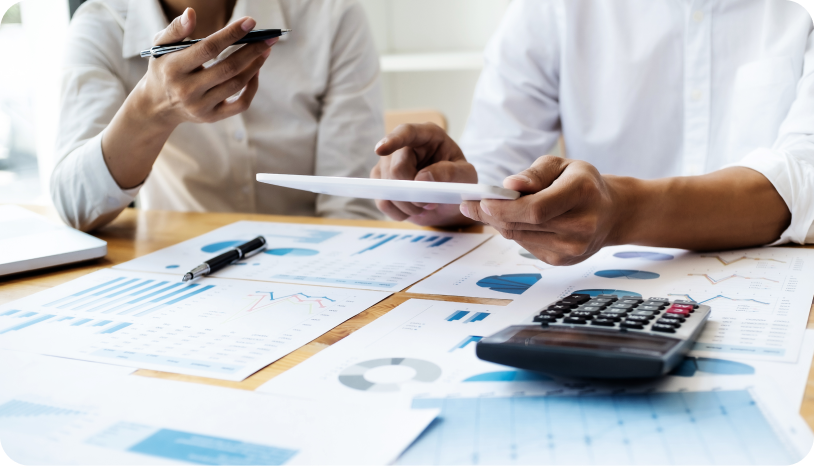
Get a Head Start on Your 2025 Taxes: Smart Tips for Small Business Owners

For businesses that rely on heavy equipment to operate, maintaining that equipment is critical to success. Taking care of your equipment can help you cut costs, save time, maintain a steady work schedule, and delay the need for equipment replacement.
However, like all equipment, heavy machinery - think: forklifts, bulldozers, trucks, and cranes - doesn't last forever. It's important to learn when to repair, rebuild, or replace construction-related equipment to ensure you're getting the maximum use out of your machinery.
Equipment replacement affects everything from your work capacity to your business' financial health, so it's crucial to weigh your options carefully. Whether you decide to repair, rebuild, or replace heavy equipment depends on five factors:
The state of your equipment is the first and most important factor to consider in a decision regarding equipment replacement vs. repair. You need to evaluate how your equipment is performing. Is it damaged, slow, or posing safety concerns? How many miles or hours has it logged? How often does it have issues? Examining the equipment's condition is key to figuring out how serious your problems are, and what you need to do to fix them.
You need to compare the cost of repairing machinery or rebuilding your equipment with the cost of replacing it. This means you have to conduct a repair vs. replace cost analysis, which would include factoring in the cost of the equipment or parts in question, plus labor, regular maintenance, preventative maintenance, disposal, and lost productivity or work time.
Sticking to a heavy equipment maintenance schedule isn't cheap, but the costs vary depending on the type and condition of your equipment. The upkeep on an older piece of equipment will be more expensive than that of a newer model, so you need to figure out how much your construction equipment maintenance costs.
Even if your current equipment works fine, there may be a newer, more advanced version of your machinery that works better. If new equipment could improve day-to-day operations, it may be worth looking into equipment replacement more carefully.
Consider how much time you can dedicate to repairing, rebuilding, or replacing your equipment. Depending on the issue, repairing can take hours or days, while rebuilding might take several days or weeks. The speed of equipment replacement, on the other hand, depends on the availability of the item you need. If you have backup machinery or can afford to pause certain projects while you rebuild or repair, you may not need to opt for full equipment replacement. On the other hand, if you don't have time to slow your work pace, you may need a quicker solution.
Repairing a piece of equipment means fixing one or two defective components. Rebuilding, on the other hand, involves changing out the fundamental parts of a piece of machinery, so you have an updated version of your equipment.
You might need a repair if a part is damaged, faulty, or inefficient. Depending on the issue, the cost of repairing machinery doesn't have to be too high and the process can be straightforward and take just a few hours, or it can be a complicated procedure that takes several days.
Rebuilding, on the other hand, generally requires more resources and is more time-intensive, taking anywhere from several days to several weeks. Many business owners choose to rebuild your heavy equipment if the foundation of the machine is good, but the piece is outdated, slow, or broken in a handful of areas.
When debating a repair or rebuild, you need to consider what will cost the least amount of money and net the best results. If the cost of repairing machinery or rebuilding is low or covered in your warranty, then you probably don't need to pursue an equipment replacement. However, if the repair costs - including labor and lost time - amount to over half of the initial cost of the equipment, it may be smarter to invest in a new piece.
You also need to ask yourself whether a repair or rebuild will successfully fix the issue and restore your equipment to its optimal state - or just act as a bandaid. Sometimes, what appears to be a small issue actually indicates a much bigger problem. If that's the case, then repairing may not save you money in the long-term as the cost of heavy equipment maintenance begins to exceed that of the repair.
Keep in mind, too, that equipment becomes more expensive over its lifetime. Minor fixes in the beginning eventually turn into greater, more costly issues as the quality of the machine deteriorates.
Heavy equipment replacement involves getting rid of your old equipment and either buying new or used equipment or parts. It's a good route to take if you have damaged, substandard, or outdated equipment that's too costly or time-consuming to fix, or if you foresee major problems with it in the future.
Sometimes, equipment replacement is less about the condition of your current item and more about the potential of a new piece. If purchasing a more advanced piece of equipment will help you work faster, simplify your equipment maintenance schedule, serve your customers better, improve operations, or otherwise set you on a path toward long-term growth, then it may be worth the splurge. However, if you'd rather put your money toward another business cost like marketing or sales, it may be better to squeeze a few more years out of your equipment by repairing or rebuilding it.
Regardless of your financial situation, equipment replacement is a major expense for any business, so it's important to review your cash flow projections, balance sheet, and income statement. From there, you can determine whether or not you're in a position to buy a new piece of equipment or look into financing.
Before you make a decision regarding equipment replacement vs. repair, take some time to analyze the numbers. Start by writing down the various costs of owning and operating your heavy equipment, including:
To compare the numbers, you also need to estimate how many years or miles you'll be able to get out of an equipment repair versus an equipment replacement.
Say, for example, that your delivery truck has a faulty engine. A brand new engine has a life expectancy of approximately 200,000 miles and costs $8,000 to replace it. Rebuilding the engine, however, costs just $3,500 with labor included and gives you approximately 100,000 miles.
In this instance of a repair vs. replace cost analysis, buying new costs significantly more than rebuilding, but it also gives you double the mileage. The option that makes the most sense for your business will depend on your cash flow, work schedule, and growth goals, in addition to the initial upfront cost.
If you need to replace your business's heavy equipment, consider heavy equipment financing. Favorable Funding Circle equipment financing rates can give you the freedom to buy the equipment your business needs without tying up all your cash. At Funding Circle, our heavy equipment loans let you borrow for up to five years, with competitive interest rates. Apply today or see how we compare to other lenders.